With good corrosion resistance, good thermal/electric conductivity and strong high-temperature stability, tungsten-molybdenum materials have become the preferred electrode materials in the fields of glass smelting, rear earth smelting, glass fibers, aluminium silicate, etc.
The significance of replacing tungsten-thorium electrodes by lanthanum-tungsten electrodes is firstly reflected in the prevention from radioactive hazards. The electric conductivity of tungsten-lanthanum 15 (with the lanthanum oxide content of 1.5%) is the most approximate to that of 2% thorium-tungsten electrodes; therefore, electric welders can conveniently and quickly replace thorium-tungsten electrodes by these electrodes without the variation of any welding procedure, thus avoiding radioactive hazards of thorium-tungsten electrodes. This transformation is easy and free no matter under AC conditions or DC conditions. Lanthanum-tungsten electrodes also have other advantages of durability in use, high current but the minimum burn-out rate.
The temperature of contact materials can be changed from zero degree centigrade to thousands of degree centigrade within several seconds when high-voltage vacuum discharge pipes are placed in workplaces. Moreover, ablation resistance, high tenacity and good electric/heat conductivity of tungsten-copper can provide necessary stable conditions for discharge pipes.
Tungsten-copper alloy electrodes are formed by combining high-purity tungsten powder with high-purity high-plasticity high-conductivity copper powder and then carrying out static pressure molding and high-temperature sintering. As electric spark molding electrodes, they have the following advantages:
1. High hardness, low consumption, reduction in electrode length;
2. High electric conductivity, high processing speed;
3. High hardness and high electric conductivity: tungsten-carbon steel materials of which common copper cannot discharge electricity can be smoothly machined;
4. High tensile strength: it is suitable for processing products in complicated shapes;
5. The integrity of copper workpieces can be kept even in long-term discharge, so the molds are high in precision;
6. Uniform texture, small contact surface losses;
7. High stability during high-speed operation;
The copper content of electrodes can be adjusted between 15% and 45% according to the requirements of customers.
Resistance welding is a method for compressing workpieces to be welded between two electrodes, adding current and heating them to a molten or plastic state by using resistance heat effects generated when the current flows through workpiece contact surfaces and adjacent areas so as to form metal binding.
-
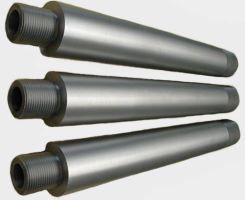
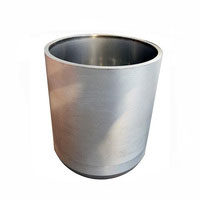
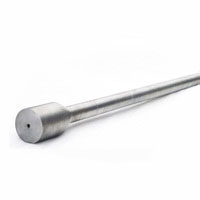
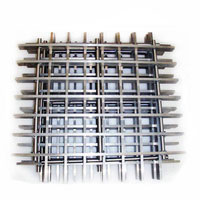